Advanced Modbus-Enabled Motorized Valves
Take control of your automation systems with our new advanced motorized valves featuring Modbus RTU RS485 and Modbus TCP support. Built for modern industry and infrastructure, these smart valves combine precision control, remote communication, and robust design, making them ideal for integration into SCADA, PLC, BMS, and IoT platforms.
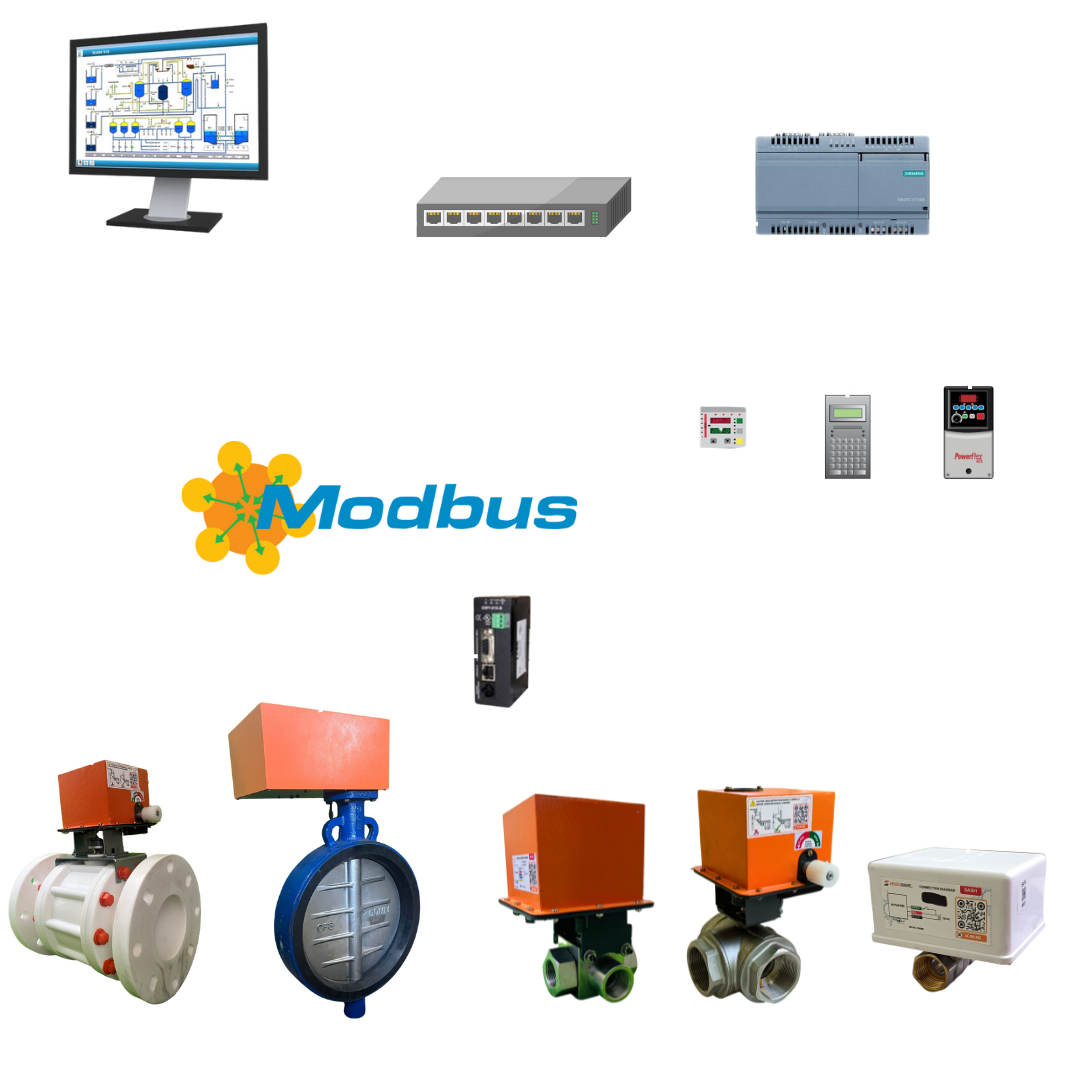
What is Modbus?
Modbus is one of the most widely used communication protocols in industrial and building automation. It was originally developed to allow electronic devices to communicate easily over a shared network. Today, it remains a reliable and cost-effective method for enabling different systems—such as sensors, controllers, and actuators—to exchange data in real time.
There are two popular types of Modbus communication:
Modbus RTU (RS485): A serial communication protocol that uses a twisted pair cable. It is ideal for long-distance, noise-resistant communication between multiple devices on the same line. Common in HVAC systems, factory automation, and energy metering.
Modbus TCP (Ethernet): A modern, IP-based version of Modbus that works over standard Ethernet networks. It supports faster data exchange, easier wiring, and direct integration with most Building Management Systems (BMS), SCADA, and IoT platforms.
By using Modbus, devices like our smart motorized valves can communicate seamlessly with your central control system—sharing real-time data such as valve position, operation status, or faults—while also accepting remote commands. Its open standard and broad compatibility make it a go-to choice for integrating equipment in smart buildings, industrial plants, water networks, and energy systems.
Key Features – Designed for Intelligent Control
Modbus RTU and TCP Support
Our motorized valves support both Modbus RTU (RS485) and Modbus TCP (Ethernet), ensuring seamless integration with a wide range of control systems. Whether connecting to BMS, SCADA, PLCs, or IoT platforms, they offer stable and reliable communication across both legacy serial networks and modern IP-based infrastructures. This flexibility makes them ideal for new installations as well as retrofitting into existing automation systems
Remote Control and Real-Time Monitoring
With built-in support for Modbus commands, our valves can be configured and managed remotely—eliminating the need for physical access during setup or troubleshooting. Operators can assign or modify slave IDs, monitor valve position (open, closed, or intermediate), receive digital feedback, and track fault or error conditions in real time. This smart connectivity helps reduce manual intervention, streamline maintenance routines, and enhance overall system efficiency.
Precision Motorized Actuation
Each valve is equipped with a precision motor and internal position tracking mechanism, ensuring accurate and smooth actuation. The high-torque motor provides reliable performance under varying pressures, while the motion control system is ideal for both throttling and simple open/close operations. This level of control is essential for applications involving flow regulation and isolation, where repeatability and precision directly impact process stability and output quality.
Integrated Feedback and Status Indication
Our valves include a built-in feedback system designed for operational clarity and fast diagnostics. Digital input signals provide real-time confirmation of valve position—such as fully open or fully closed—allowing systems to validate performance without additional sensors. An onboard status LED adds a visual layer of feedback by indicating current operational status or highlighting error conditions, helping maintenance teams respond quickly and accurately when issues arise. This integrated feedback simplifies system design and enhances overall reliability.
Seamless Integration Across Applications
Designed for versatility, these smart valves integrate seamlessly across a wide range of industries and control systems. In industrial automation, they manage fluid handling, dosing, and shut-off control. HVAC systems use them to regulate air and water flow for temperature control. Smart water networks benefit from their precision in pressure balancing and leak detection, while energy platforms use them for renewable system control and thermal loop optimization. Standard Modbus protocols ensure broad compatibility with most automation ecosystems.
Durable and Customizable
Built for continuous performance in demanding conditions, our valves feature rugged housing that resists vibration, dust, and moisture, along with thermal stability for reliable operation in extreme temperatures. The high-duty cycle design supports frequent actuation without compromising longevity. To meet diverse requirements, we offer customization in body materials (brass or stainless steel), valve sizes, I/O configurations, and Modbus register mappings. Custom logic profiles can also be provided to match specific application needs.
How to connect our Modbus-Enabled Motorized Valves to a BMS using Modbus
Power the Valve
Connect the valve to its recommended power supply to activate internal controls and communication features.
Choose Communication Type
For Modbus RTU, connect the RS485 terminals (A/B) to your controller’s serial port.
For Modbus TCP, plug in the Ethernet cable to your network switch or directly to your BMS controller.
Set the Communication Parameters
For Modbus RTU: The valve comes with a default slave ID and communication settings. You can update the slave ID, later via Modbus commands—no DIP switches required.
For Modbus TCP: Ensure the device has a valid IP address and port on your network via DHCP.
Map the Registers
Refer to our valve’s Modbus register map to connect status, control, and feedback registers to the BMS system points.
Test the Communication
Use your BMS software or a Modbus testing tool to verify communication. You should be able to read valve position, feedback inputs, and control the valve remotely.
Finalize Integration
Add valve control logic to your BMS interface. You can now monitor and control the valve as part of your automated system.
Follow our Social Channels